
Carry Collaborations
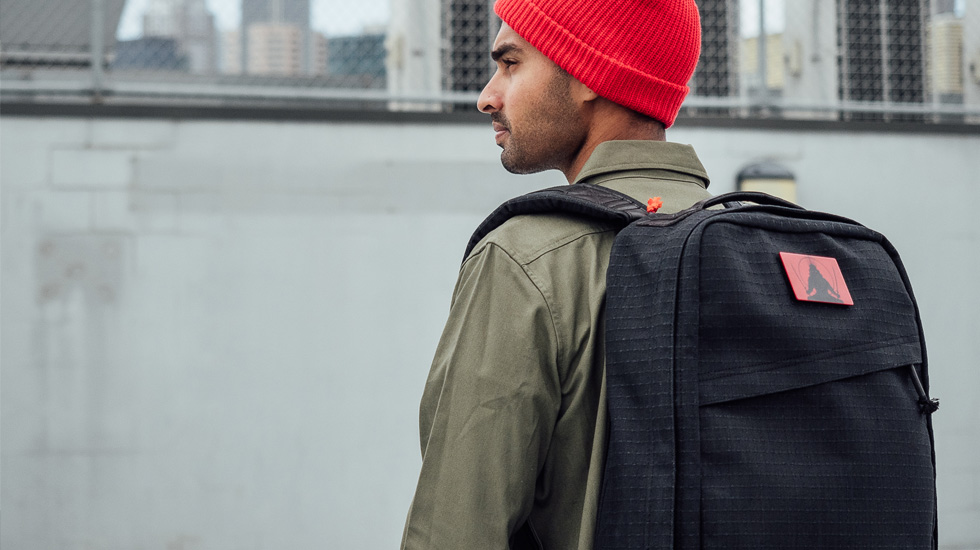
CARRY COLLAB XXXIV
GORUCK x Carryology GRXC2 Samurai | Exclusive Release
The second-coming of the GRXC Program.
A pack inspired by the fierce samurai warriors of Japan’s past.
Built with a fully custom, made-in-Japan, Black Samurai Sashiko Denim, then enhanced by Dimension Polyant’s sailcloth lamination technology for waterproofness and durability.
Featuring an exclusive one-off morale patch, designed by Jiro Yaguchi of Onizuka Tattoo in Los Angeles, and handmade via centuries-old traditional techniques in Kyoto, Japan by the world's number one samurai armor craftsman, Tatsuhito Imamura-san.
Introducing the GORUCK x Carryology GRXC2 Samurai GR1
< < < ORDER GRXC2 SAMURAI NOW > > >
SPECS
21L Dimensions: 11.5″W x 18″H x 5.5″D
21L Weight: 3.05 LBS
26L Dimensions: 12″W x 20″H x 6.75″D
26L Weight: 3.4 LBS
Laptop Protection (21L): Fits most 15″ laptops
Laptop Protection (26L): Fits most 16″ laptops
FEATURES
Built from a completely custom technical fabric: JPXDP 17oz Black Samurai Sashiko. A collaboration between Japan Blue Co. Ltd. and Dimension Polyant. Custom-made 15.5oz black x black sashiko denim, made in Japan, and laminated by Dimension Polyant for waterproofness and durability.
Black leather base, grab handle, and shoulder strap details.
PALS webbing on extra-padded shoulder straps.
Quick-access pocket.
Redesigned rainflap for ease of use – denim will break in to be ultra smooth.
500D on inner shoulder straps and back panel.
Custom Auxikko geometric pattern printed on hi-vis red 500D Cordura nylon.
YKK zippers with glove-friendly Japanese braided silk rope zipper pullers.
Samurai artwork designed by Jiro Yaguchi of Onizuka Tattoo in Los Angeles.
Morale patch handmade by Tatsuhito Imamura-san of Kyoto Armor in Japan.
Backed by GORUCK’s Scars Lifetime Guarantee.
RONIN BLOODLINE
Why samurai? There are nearly infinite warriors to choose from when we’re referencing the pages of history and the endless folds of the human imagination (folklore, mythology, movies, comics, novels, cartoons, etc.). Selecting a suitable inspiration isn’t a science, but we did consider the previous GRXC1’s character in the process. “Guerrilla X”, our fictional soldier from the future was brought to life via Dan Matsuda’s illustration. The sci-fi future backstory of the character led to the selection of high-tech materials and manufacturing processes like Dyneema, titanium, and laser engraving.
For GRXC2, we aimed in the polar opposite direction: a well-known, nonfictional, warrior from history. As a child growing up, I loved watching action movies from decades before I was born. While I had many different favorites, I was always entranced by old black-and-white samurai films such as Harakiri, Throne of Blood, The Sword of Doom, Seven Samurai (currently playing in the background as I type these words), and many more. I had samurai action figures. I vaguely remember having some thin black slippers that I used to call my “ninja samurai shoes” as a young boy for some odd reason. Who knows, man. To this day, one of my favorite literary subjects is the ancient samurai and their lifestyle. It’s endlessly fascinating. And so it was an easy choice. GRXC2 is based on the samurai, one of the most iconic warriors to ever roam the planet.
LEGACY OF JAPANESE DESIGN
As you can imagine, an all-steel or all-samurai-armor GR1 just isn’t realistic. For all of the reasons.
So I researched the clothing that samurai wore underneath their iconic armor, called Yoroi Hitatare (essentially a shirt and pants). These would be worn for comfort, as iron plates against the skin would not be very comfortable to wear into battle. Traditionally, these garments would be made from either cotton or linen, depending on the region’s temperature for successful growing of either crop, hemp in the north and cotton in the south. When these battle uniforms were damaged by wear or an opposing foe, they would not be discarded. They would be repaired.
There is a Japanese repair process that focuses on fabric, called sashiko, translating to “little stabs”. This craft dates back to Japan’s 17th century Edo Period, the particular time where samurai rose to their peak in power, fame, and wealth. The sashiko process uses a thick thread to join two layers of fabric together, each short stab and weave done by hand with a needle. This process makes the fabric stronger and more durable so samurai could wear their Yoroi Hitatare another day.
THE LORDS OF DENIM
Inspired by the samurai’s Yoroi Hitatare, I sought to use the best example of Japanese cotton fabric for the GRXC2’s exterior. Luckily, if there is one country in the world that holds the crown for expertise in the manufacturing of cotton in its tough everyday form of denim, it’s Japan. For decades, Japan has been the leader of traditionally made selvedge denim on old Toyoda shuttle looms as well as paving the way in denim innovation.
Japan Blue Co. Ltd. is located in the sleepy coastal town of Kojima which is famously known for high-end textile manufacturing, and is considered one of the top denim mills in the world. For those in the know, the legendary Momotaro (founded in 2005) denim brand is under the umbrella of the Japan Blue Co. Ltd. group (founded in 1992) as well as Japan Blue’s eponymous denim brand (founded in 2010). Both brands are the only two denim brands in the world that produce everything under the same roof, from start to finish.
From cotton harvesting, to spinning thread, to weaving the denim, dyeing, cutting, manufacturing. Everything. This is top-tier stuff, second to none. And they were interested in my ridiculous request… to develop a custom denim to some incredibly demanding and exacting specifications.
The specifications were based on performance first, aesthetics second. No compromise. If Japan Blue couldn’t hit the mark, the fabric wouldn’t be suitable for a 'GORUCK' backpack that could go tackle the rigors of daily carry.
I required a 15oz (absolute minimum) final weight, per square yard. Black on black. And finally, with an additional sashiko stitching process added to the base fabric. While this is somewhat technical talk, to put it in layman’s terms, this is an incredibly difficult ask. Frankly, this is impossible for most mills. I was surprised when they even agreed to try.
Weeks later, the first swatches came back, with different sashiko stitch patterns and variations to choose from. The only problem? They were all only 11oz denim and some were even less. But anything less than 15oz wouldn’t suffice for this project. Politely I pleaded one last time to push the mill into the unknown, thanking my contact for all of his hard work, telling him if we didn’t hit the 15oz minimum weight… all this work would be for nothing.
A few weeks later… a sample swatch arrived.
Black on black Japanese denim, with sashiko “X” stitches in heavy black thread.
And it was 15.5oz heavyweight.
Approved for production.
Success, we did it!
But… you all know we didn't stop there…
JAPANESE DENIM, ELEVATED
Unless you’ve been living under a rock since the 1860s, you’re probably familiar with denim jeans. Denim breaks in, gets softer to the touch, all while still remaining tough for everyday and outdoor activities. But for a backpack? It soaks up water like the cotton sponge that it is. And our custom-made Japanese sashiko denim? There’s even more of it than your traditional denim jeans, 15.5oz of cotton sponge to be exact, all ready to soak up rainfall. So this is when this fabric gets wild and technical and groundbreaking.
I reached out to my waterproofing textile expert friend, located 7,000 miles away from the Japanese denim mill, in a small town in Connecticut. His name is Taylor North and he’s the Head of Technical Fabrics at Dimension Polyant. We had all this traditional custom-made denim and now it needed advanced technical processes to make it perfect.
What we asked for was lamination and a DWR face finish so our custom denim would be properly waterproof. Not water resistant, but waterproof. Taylor North came up with the ultimate recipe and process to bring it to the next level. Nerd technical talk ahead, be warned:
On the back of the fabric we use a 50d solution-dyed black polyester taffeta fabric. Between the taffeta and the denim face fabric is a 0.25mil Dimension Polyant film to make the fabric 100% waterproof and provide performance by way of stability, and the unique X-Pac hand feel. It’s bonded together with Dimension Polyant’s (proprietary) Performance Adhesive, which is a high-performance thermoset (permanent) adhesive system – think a two-part chemically cured system. As opposed to a thermo-plastic (think hot glue) or water-based (think Elmer’s glue) system. Simply the highest quality adhesive available for lamination. The same adhesive that has been refined in Dimension Polyant’s yacht sailcloth for decades.
On the surface of the denim, we top-coated the denim face fabric, again with Dimension Polyant’s Performance Coating to increase the durability and abrasion resistance of the face fabric. The final step is a DWR (durable water repellent coating) that overachieves when it comes to durability and water, dirt, and oil repellency. This custom DWR was developed with a Connecticut-based company near Dimension Polyant HQ.
The result? A fabric that is waterproof, even more durable and even stronger (an impressive 290lbs/in tensile strength in warp and 250lbs/in tensile in the weft), weighing in at a hefty 17oz per yard. A traditionally made heavyweight sashiko denim made by the experts at Japan Blue in Kojito, Japan and then elevated into a performance fabric of the future by the technical scientist masters of Dimension Polyant in Putnam, Connecticut, USA.
Like denim jeans, this fabric will develop its own fades, stacks, and patina which are unique to the life and activities of each unique owner.
Looking forward, we are incredibly excited to see the different wear patterns from users around the world in the coming months and years as these packs go on adventures with you. #GRXC2Fades, anyone?
All in all, this fabric took 19+ months of development from start to finish.
It took two expert teams at two different suppliers from Japan and USA.
It’s more than 10X more expensive than 500D Cordura nylon.
It’s more expensive than Challenge ULTRA 800.
It’s more expensive than Dimension Polyant X-Pac X50 Tactical.
It’s more expensive than Dyneema CT5K.18/wov.32c.
It will never be produced again.
We call it…
JPXDP 17oz Black Samurai Sashiko.
TIMELESSNESS OF LEATHER
To aesthetically, historically, and structurally complement this black-on-black custom performance denim, we add leather. Samurai used leather as part of their armor system because it was tough and flexible.
On the GRXC2 Samurai, leather features on the pack’s entire bottom panel, the padded grab handle, and the shoulder strap attachment (over top of the webbing).
This smooth grain leather feels buttery soft against the skin but remains extremely burly. Just like the JPXDP 17oz Black Samurai Sashiko, it will age beautifully, no matter what you throw at it.
AUXIKKO LINER
To line the pack, we wanted something that would be water-resistant against spills, durable, and tough.
It was unanimous, we selected Cordura’s 500D nylon for the liner, a fabric tougher than some brands use for the exterior pack fabric.
Normally, we opt for a bright orange liner. But not this time. In homage to the theme, we selected an iconic samurai color, vibrant red.
And then… we had the fabric printed with our own custom-designed Carryology geometric pattern called auxikko. Our design is directly inspired by the Japanese geometric pattern kikko, which is the word for samurai armor plates as well as the word for the pattern of a tortoise shell, both being visually similar to one another.
Custom auxikko-printed high-vis samurai-red Cordura 500D nylon liner, done.
SMOOTH AS SILK
GORUCK’s zipper pullers are some of my favorites in the game. They’re ultra-minimal, strong, and work well with gloves. So we didn’t want to reinvent the wheel. But 550 nylon paracord hanging against our JPXDP 17oz Black Samurai Sashiko just didn’t make much sense visually or in concept. However, Samurai would use braided silk rope to attach various pieces of armor to one another, keeping it all together in a protective, easy-moving, and evil-looking suit.
Why silk? Well, they didn’t have Fidlocks or Cobra buckles back then. Silk was relatively abundant in Japan at the time, even if it took some effort to produce. Pound for pound, it’s stronger than steel. How strong? Here’s some fancy math numbers. Typical commercial silkworm silk has a tensile strength of about 0.5 gigapascals (GPa), a breaking elongation of 15%, and a breaking energy (toughness) of 6 × 104 J kg−1. Aside from its strength, it’s incredibly soft against the skin and flexible too. Basically, braided silk rope is the grandfather of 550 nylon paracord that we use today.
We hunted down a specialty supplier in Japan which was no easy task, then did some strength testing and color approvals. We loved it and selected black and then red for the internal label pocket and the exterior quick-access pocket. Of course, we did the same shrink wrap like the OG, to keep it all tidy and glove-friendly. And as a nod to custom, we made the ends of the rope extra fluffy, just as the samurai did. All the benefits of the original GORUCK paracord zipper pullers, with a performance luxury silk twist.
MORALE AND ANCIENT ARMOR
Our challenge here was to better the GRX1’s patch. A patch designed by Dan Matsuda and laser engraved by Marc Mummert on titanium. It was no small feat, but the result is something we’re incredibly proud of.
THE ARTIST
Jiro Yaguchi was born and raised in Japan, is now a Los Angeles resident, and is an incredibly talented artist to a level of fame, and resident tattooer of Onizuka Tattoo. Wanting to adorn his inkwork on your body? Prepare for many months to wait for his first availability. Possibly even longer than a year.
Jiro-san's design is bold. A red background with a fierce black silhouette. He included many different references in his small but impactful piece of art. First, his overall inspiration came from samurai movie posters from the 1950s-1970s. He specifically mentioned posters for films made by Akira Kurosawa, who is widely regarded as one of the most important and influential filmmakers in the history of cinema (Seven Samurai, Throne of Blood, Sanjuro, among many, many more).
For the character himself, he blended two of his favorite samurai warriors. The most eye-catching element on the design for most is likely that wild-looking helmet. For folks who know their samurai history, yep, you guessed it, that’s Toyotomi Hideyoshi’s iconic helmet. Known as the man who unified Japan, he came from a simple peasant background and eventually became the de facto leader of Japan and acquired the prestigious positions of Chancellor of the Realm and Imperial Regent by the mid-1580s. Jiro-san has a particular fondness for Toyotomi, with a replica helmet of his located in his tattoo studio, which he showed me when I visited (bottom right of the image above).
The other samurai inspiration, none other than Miyamoto Musashi. He was not officially a samurai as he never held his own lands or served a lord as a formal samurai, but as a duelist, none can compare to Musashi. Arguably the best swordsman to ever walk the face of the earth. Undefeated across at least 60 duels, he founded multiple schools of swordsmanship and, later in life, wrote The Book of Five Rings, which is still read today for insight into his tactics and philosophy.
The visual element that represents Musashi is the iconic dual swords he is wielding, as he was the first to invent this method of swordsmanship.
In 1612 he fought his most famous duel, which was against Sasaki Kojiro, known as “The Demon of the Western Provinces” and considered the greatest swordsman of the time. Musashi aggravated his opponent by intentionally arriving at the tiny island of Funajima, the mutually agreed-upon battleground… nearly three hours late. In the course of a fierce but brief duel, he struck his katana-wielding enemy dead using nothing but a wooden sword he’d carved from an oar on his way to the island.
THE ARTISAN
This part still gives me chills. Every component of the GRXC2 Samurai was in place, but we were missing the final critical element… who would physically bring this artwork to life? And how would they do it? It had to be a method that paired with the concept.
Tatsuhito Imamura-san of Kyoto Armor is located in Kyoto, Japan. Tatsuhito-san is recognized by the government of Japan, officially certified by the Minister of Economy, Trade and Industry as a Traditional Artisan. His craft has been passed down from generation to generation, a lifelong dedication to doing things the old way. He is considered the best living samurai armor maker in the world.
Tatsuhito-san has made each patch by hand, using 2”x3” raw iron plates and then coated with an epoxy-like coating that is hand-harvested from the sap of the Japanese lacquer tree (Toxicodendron vernicifluum). If this sounds somewhat familiar, this is the traditional urushi-e method. Urushi-e (or Japanese lacquerware) offers a finish that is very durable and resistant to water, acids, and heat. While it might be primitive, this genius process was centuries ahead of its time, as there is some deep science behind it. The tree sap actually has a chemical reaction with the iron, permanently bonding to it and making the iron stronger. This artform is incredibly difficult and requires many slow meticulous steps to perfect. But the end result? Vibrant reds that trick your eye into thinking you're holding a digitally photoshopped image in your hand. And an infinitely rich and deep black that goes on forever.
Tatsuhito-san explained this is the exact method by which samurai armor has been made for centuries. And funny, our 2”x3” patch sizing is even the approximate size of a single scale of armor, which would be overlapping other small armor scales, attached together via braided silk rope. Essentially, it is the same as a piece of samurai armor.
Handmade samurai armor morale patches, made by the world’s best samurai armor maker, Tatsuhito Imamura-san of Kyoto Armor.
Note: While this traditional handmade-in-Kyoto armor scale has extremely high strength properties, it has a highly hand-polished gloss surface that will show scuffs and marks if rubbed up against hard/textured surfaces.
Safely store it away or put it on display behind glass to keep it in perfectly mint condition. Or let it develop a battle-worn patina from your worldly adventures. The choice is yours.
MADE IN THE USA
Introducing the GORUCK x Carryology GRXC2 Samurai GR1.
Based on the Carry Awards Hall of Fame winner, GR1 backpack. And the second chapter of the GRXC project with GORUCK and Carryology.
Inspired by the Samurai warrior. Made in the USA with Japanese and USA materials.
One-time release only, never to be repeated.
GR1 21L and GR1 26L sizes are both available.
< < < ORDER GRXC2 SAMURAI NOW > > >
GORUCK will ship internationally.
___
EXCLUSIVE RETAIL PARTNERS
Launching various drop times. Please visit retailers' social channels for specific drop times.