How to Choose the Right Backpack Fabric
It’s fair to say that Kevin Dee is a bit of a fabric genius. Well versed in product design and hands-on sewn goods, Kevin is the co-founder of crossover carry brand EVERGOODS, and over the years has honed his skills by running his own sewing shop and as an R&D Engineer at Patagonia. So talking fabrics in relation to backpacks? It’s kinda his jam.
So we asked Kevin to share his textile expertise, so we can learn a little, brands and customers alike, about how to choose the right backpack fabric for you. Enjoy!
What are some of the things that go into producing a backpack fabric or textile? And how do you know a good one when you see it? What does “good” even mean in terms of backpack textiles? Unfortunately, the straight answer is that there is no straight answer. There are many steps involved in the production of finished textile, and with variables that affect the outcome at every stage, evaluating them can be a daunting task. Here I’ll share a look inside EVERGOODS’ textile selection process with insight for designers and consumers.
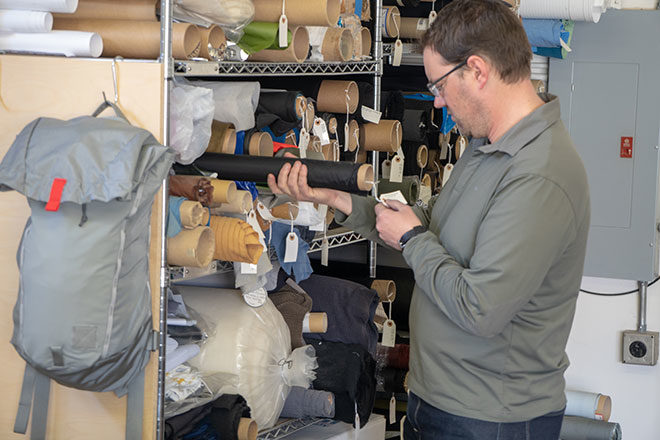
The critical first step is to identify what the priorities are for the product. These may be performance-related things like durability, weight or weatherproof-ness. They may be considerations of taste and perception like visual aesthetic, hand feel, or tradename recognition. Or they may be practical and operational concerns like cost, country of origin, environmental impact or any other thing you care to identify as a priority. Once you’ve compiled your list of wants, try to understand them in order of importance. You’ll never get everything you want from a single material, so be realistic about the priorities. For EVERGOODS’ main body fabrics Jack and I were primarily interested in longevity and durability*, a perception of high quality and attention to detail, and a clean and timeless aesthetic.
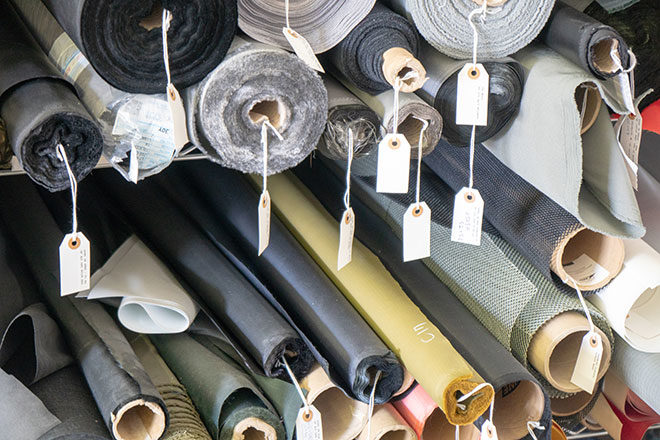
*A note about “durability” – There must be a dozen ways to try to quantify this. At EVERGOODS we feel that for our product, the most relevant measures of durability are abrasion resistance, pick resistance and resistance to seam slippage (a common seam failure in looser, lower density weaves where the yarns get pulled off a fabric’s cut edge). Other measurable characteristics include tensile strength, tear strength, cut resistance, puncture resistance, heat resistance, UV resistance, wet flex performance, cold crack performance and on and on. There seems no end to the conditions under which something might physically fail.
“Once you’ve compiled your list of wants, try to understand them in order of importance. You’ll never get everything you want from a single material, so be realistic about the priorities.”
At this point it’s really helpful to cultivate a basic knowledge of textiles’ components and variables so you can narrow the search. Whether you’re a designer meeting with a fabric vendor, or a discerning customer looking at a wall of backpacks, the more specifically you understand what you’re looking for, the better your ability to evaluate and find that needle in the haystack. The most basic component of a textile is the fiber, the tiny individual strands of material that make up the cloth. What fiber is the textile made of and what characteristics does this impart to the finished product?
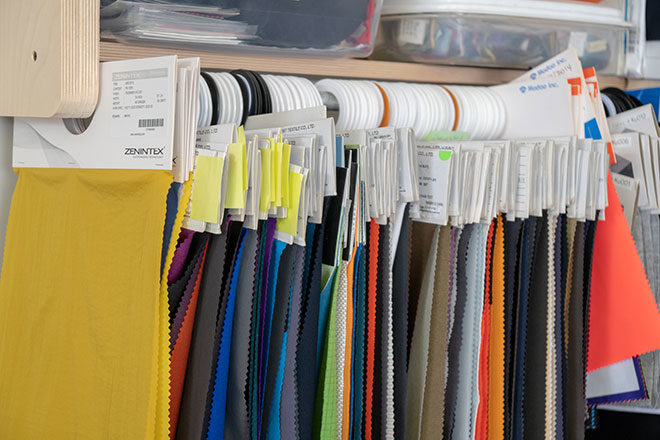
Fiber
EVERGOODS works with Nylon 6,6, a higher tenacity, longer-chain polymer in the Nylon family that is 20% more abrasion resistant and has 15% higher tear and tensile strengths than conventional nylon. The 6,6 formulation we use is produced by Invista, and so could be branded with the Cordura* name, but EVERGOODS prefers to maintain an uncluttered aesthetic with minimal branding and logos, so we don’t include a Cordura label on our product.
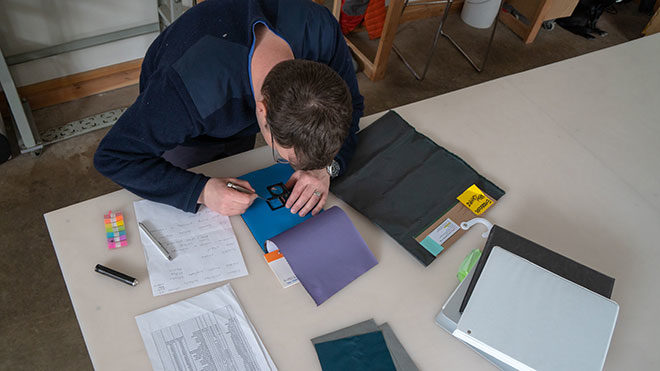
*A note about Cordura – When most folks talk about “Cordura”, they’re referring to the air-textured nylon cloth popularized in the 1980’s. It was available in typical weights of 1000 denier and 500 denier and renowned for its durability in backpacks and equipment. These days the tradename Cordura can legally be applied to any textile containing yarn produced by parent company Invista. Cordura-branded fabric comes out of mills all over the world, is available in many weights and constructions, gets blended into apparel textiles and pops up anywhere that marketers believe the name and added cost will imply “durability” in the mind of the target consumer. Unfortunately, identifying something as “1000d Cordura” helps narrow the field, but in no way identifies a specific or singular textile.
Polyester – Compared to nylon, polyester is less expensive and also generally less durable. Polyester has inherent UV resistance and is hydrophobic (absorbs no water), making it appropriate for applications like rafting gear or tent awnings that may encounter days and weeks of exposure to direct sunlight or submersion in water. Polyester is highly recyclable and can be dyed using waterless methods, potentially giving it some environmental benefits. And its lower cost and affinity for digital printing techniques such as dye sublimation lends it to markets like fast fashion or children’s backpacks where a wide variety of colors and prints is desired at lower volumes and costs.
“These days the tradename Cordura can legally be applied to any textile containing yarn produced by parent company Invista. Cordura-branded fabric comes out of mills all over the world and is available in many weights and constructions.”
Nylon – Since the 1970’s nylon has been the go-to staple of backpack and luggage design. This “modern” textile is lighter, stronger and more weather and rot resistant than its cotton predecessor. It’s also generally more durable than polyester without being astronomically more expensive. Nylon can weaken with prolonged exposure to UV or while saturated for extended periods. Nylon can also be dyed to nearly any color standard, although nylon 6,6 often shows a streaking effect in lighter colors due to uneven dyeing of its extremely long polymer chains.
UHMw PE – Ultra High Molecular Weight Polyethylene is more commonly known by its tradenames Dyneema© and Spectra©. It’s basically a super long-chain formulation of polyethylene that was originally used in industrial, medical and defense applications, but has seen an increasing presence in the sports and outdoor markets over the past 20 years, introduced primarily through its use in sailing. The Dyneema name carries a lot of weight due to its extremely high tensile and tear strengths (stronger than steel by weight), and exceptional abrasion resistance. It occupies a highly technical, NASA-like position, with costs that match. The strength and durability of this fiber is without question. Even at incredibly high loads, Dyneema exhibits zero stretch, making it appropriate for bulletproof vests and racing sails where energy transfer is critical. In addition to being UV resistant and hydrophobic it is also highly chemical resistant. In fact, Dyneema is so impenetrable that it cannot be dyed by conventional means. Traditionally white, and more recently offered in black with additional colors in the works, Dyneema is restricted to a more limited visual palette than more conventional fibers. It can also present assembly challenges resulting from Dyneema’s relatively low melting point and low coefficient of friction. In short, UHMw PE satisfies the desire for a strong, highly technical material with a tougher-than-steel reputation, but not without some trade-offs.
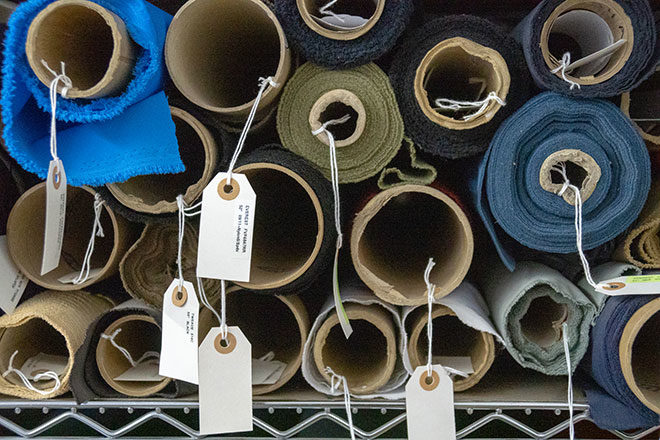
Yarn
Once the fibers are produced, they get made into yarn. Yarn is basically a bundle of fiber that gets wound onto spools in preparation for weaving or knitting. The yarn can be twisted or straight, be processed for different amounts of luster, and comes in many different diameters designated by denier. “Denier” is a very old textile word originally having to do with yarn weight (I’m sure you can look it up), but I basically take it as a relative indicator of a yarn’s diameter or thickness. Common deniers for backpack textiles are 210, 420, 500, 1000 and 1680 (ballistic*). Thicker yarns have more fiber material in them, so as a general rule, higher deniers will yield higher abrasion resistance. However, other important factors such as fiber type, weave pattern and weave density also play an important role.
*a note about 1680d – Nylon in this weight is commonly known as “ballistic” nylon because it was first used in early attempts at soft body armor (pre-Kevlar). 1680 makes burly fabric and is most commonly found in airline luggage, haul bags and other heavy-use items. The whole point of 1680 is rugged durability, so these are generally nylon. Of course, 1680d polyester also exists because it looks just like nylon but costs less (and wears out faster). Similar to Cordura, “ballistic nylon” used to be a specific raw material, but is now more of a general descriptor.
“Thicker yarns have more fiber material in them, so as a general rule, higher deniers will yield higher abrasion resistance. However, other important factors such as fiber type, weave pattern and weave density also play an important role.”
There are several ways that synthetic fibers can be produced. Most commonly they come out of a spinneret, like a tiny plastic extrusion. Untreated yarn in this form is known as “bright” yarn because its smooth plastic filaments reflect a fair amount of light. This bright yarn is the most abrasion resistant, which is why it is the preferred choice for modern mountain sports. “Dull” yarn undergoes a chemical scouring treatment that microscopically pits the surface to scatter light, slightly weakening it in the process. Another treatment commonly associated with traditional Cordura is air-texturing. In this process the yarn bundle passes by a hot air jet that lightly “frizzes” the fibers. Air-textured yarn gives the finished textile a bit more bulk in the hand and also scatters light for a dull appearance without degrading its strength. EVERGOODS uses 420d bright yarns in its Mountain products and 500d air-textured yarns in its Civic products.
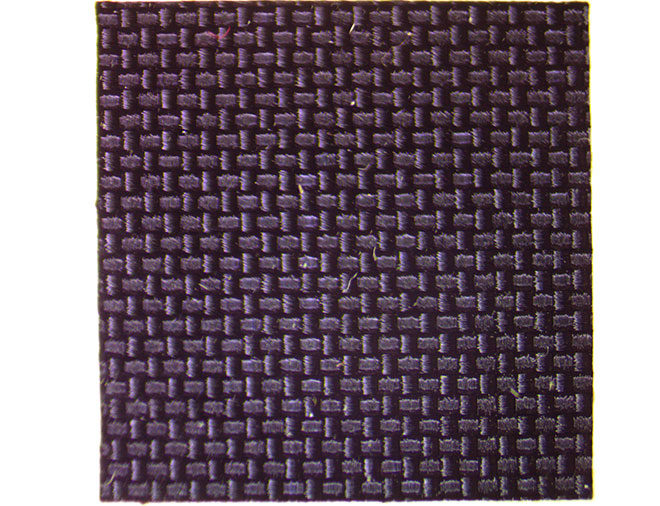
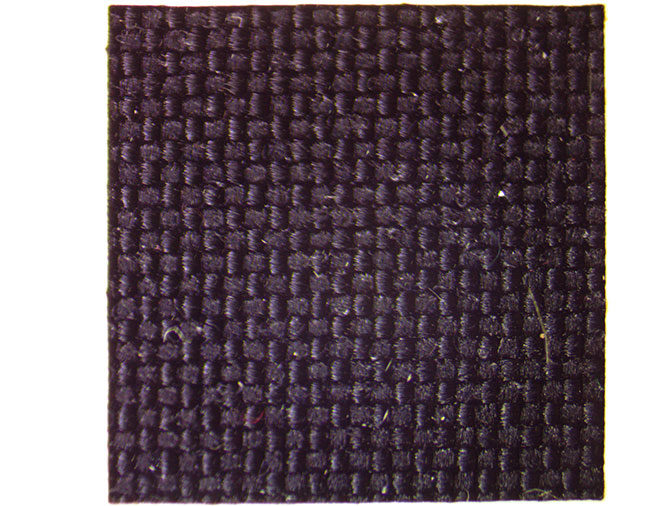
Weave
The next phase of textile production is the weaving. The vast majority of backpacks use woven textiles (rather than knits or non-wovens, though these are not unheard of). Weaving is done on a loom and involves intertwining a set of vertical yarns called the warp, with a set of perpendicular yarns called the weft or fill. EVERGOODS uses balanced, plain weave fabrics with the same density of warp and weft yarns for equal strength in both directions. The majority of backpack fabrics however are unbalanced for reasons of cost savings. Weave density is determined by counting the number of yarns in one square inch of warp and weft and multiplying them together. In general, higher weave densities yield stronger fabrics and more yarn intersections yield stiffer, more pick and abrasion-resistant fabrics. However, overly-stiff constructions start to have lower tear strengths, so there is a limit to how much stiffness is desirable. There are endless variations in weave, but to illustrate how these factors work together let’s look at three of the most common examples, a plain weave, a ripstop and a twill.
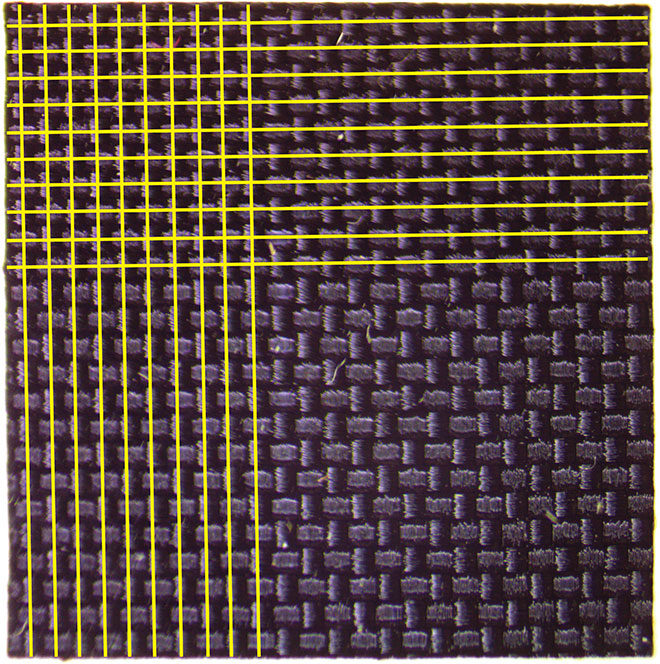
The most basic weave pattern is called plain weave, also known as “1 by 1” because every fill yarn intersects with every warp yarn. One result of this high number of yarn intersections is that no single yarn is exposed for any great distance, making it less available to surface abrasion and locking it together with the surrounding yarns so that the sharp end of a thorn or wire can’t get underneath and pick at it. This interconnectedness, combined with a high thread count results in less seam slippage and also creates a stiffer finished product. Stiffer textiles are more prone to tearing because force is better able to focus on a single yarn and break it at an isolated spot. In weaves where yarns can shift and move slightly, a tearing force gets spread across a longer length of yarn, spreading and dissipating the energy and increasing the textile’s capacity to absorb the force rather than tearing. For the sake of product differentiation brands seek out (and mills offer) decorative weaves galore, but the plain weave is still the general purpose workhorse of the backpack world.
A common variation on plain weave is the well-known ripstop. The simplest ripstop is basically a plain weave, except that by skipping intersections at regular intervals a grid of double yarns is created in the weave. So, a 210d textile may have a grid of what are essentially 420d rip yarns. Because these two yarns are not isolated from each other by alternating intersections, they act as one, moving together, combining their tensile strengths and spreading force along their length. As the name implies, the purpose of this construction is to regularly confront any tearing force with a double strength yarn. The downside to this construction is that these larger yarns stand more prominently on the textile’s surface, creating crowns that are more exposed to abrasion and picking. Backpack rips most often propagate from some initial cut or pierce in the fabric by a sharp object like an ice tool or crampon. For this reason ripstop is most appropriate for activities that are likely to encounter sharp edges or points like mountaineering. It is also an easy way for brands to add a more “technical” aesthetic to a product.
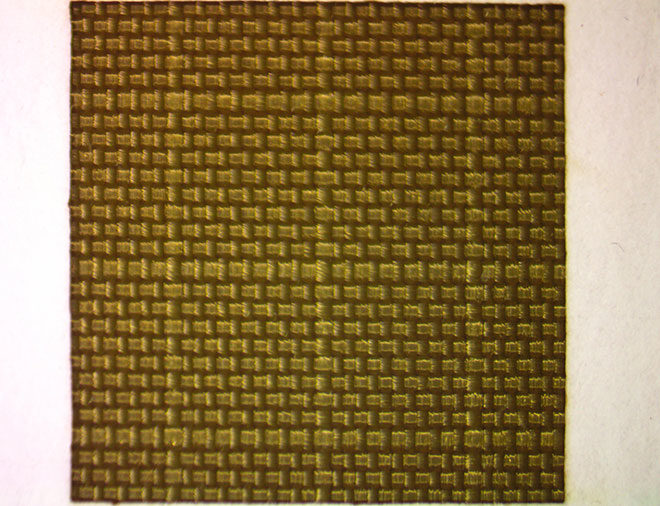
A third common weave is twill. Where plain weave makes an intersection at every yarn, twill makes an intersection after every two yarns. Controlling where these skips and intersections occur creates common patterns like busted twill and herringbone, but these are all twills. These skipped intersections or “floats” are more exposed to picking, but they abrade evenly because they are consistent across the textile’s surface. Twills have half the number of intersections compared to plain weaves, allowing more shift between the yarns. This makes them more prone to seam slippage, but also yields a softer hand and higher tear strength, making twill a popular weave for apparel like jeans because it combines durability with comfort. This weave is less common in backpacks, but included here to illustrate how weave characteristics can affect textile performance.
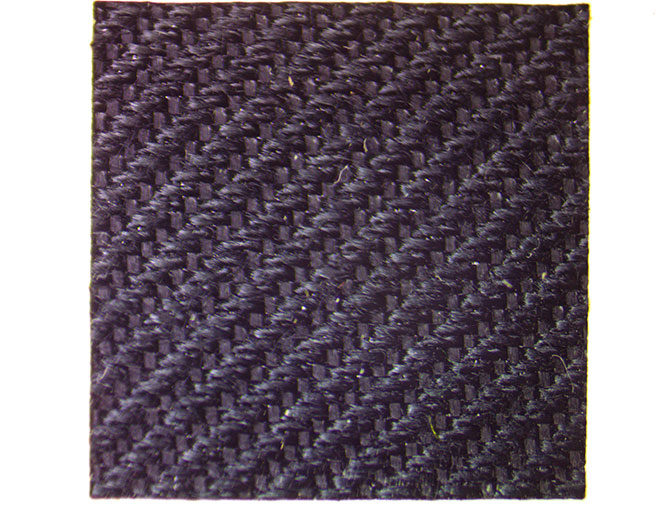
“In general, higher weave densities yield stronger fabrics and more yarn intersections yield stiffer, more pick and abrasion-resistant fabrics. However, overly-stiff constructions start to have lower tear strengths, so there is a limit to how much stiffness is desirable.”
As you can see, all these factors work in connection with each other, and strengthening one characteristic often comes at the expense of another. This is by no means a comprehensive list of all the steps and variables that add up to create textile. Indeed, after weaving most textiles undergo one or more finishing treatments like coating or lamination, adding yet another layer of variables. Hopefully, this essay has shed some light on your next fabric encounter or helped you contemplate the fabrics around you in a deeper way. More than anything, I think it’s important to realize that there is no “best” textile, only the textile that best meets a narrow set of criteria as defined by the opinions and perspectives of individual users or designers.
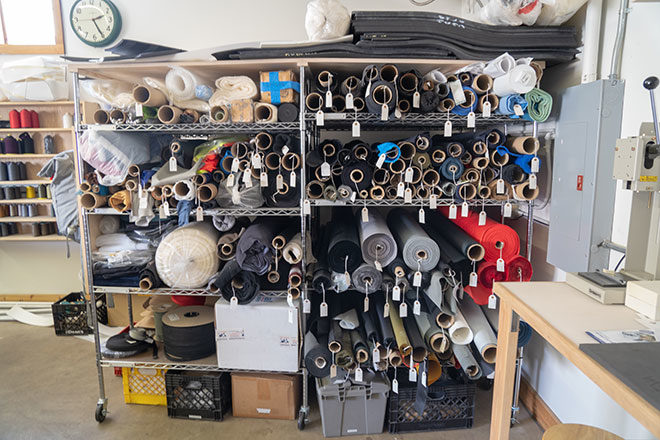
Liked this article? You might enjoy these too:
QWSTION: Is Bananatex the Next Miracle Backpack Fabric?
Dyneema vs X-Pac: Ultralight Fabrics
Ballistic Nylon vs CORDURA: Heavy-Duty Durable Fabrics